Applying Engineering Expertise To Optimising Efficiency Of Offshore Terminals
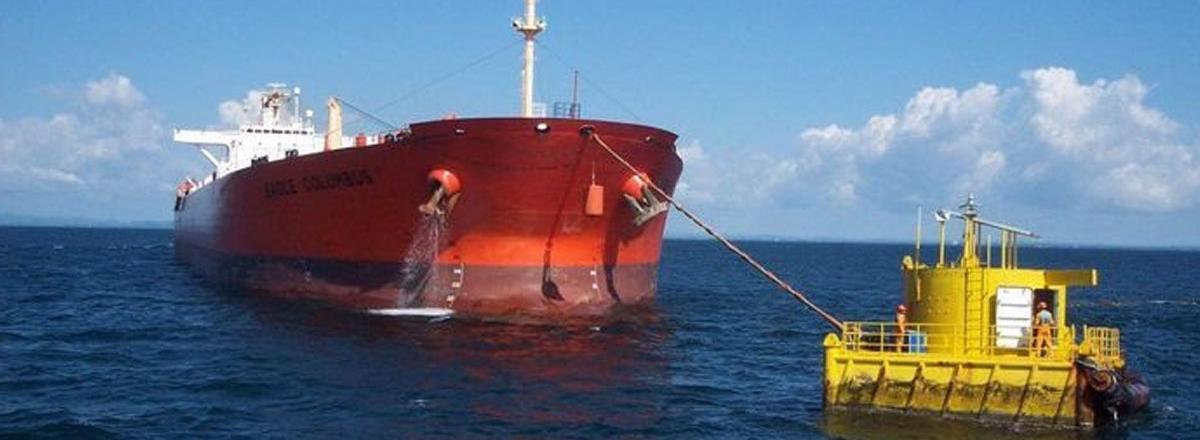
Mark Venables, CONTRIBUTOR
Jun 30, 2018 1:47 PM 129
The development of loading buoys started after the first world war when the growth in tanker sizes demanded the extension of harbor facilities into deeper water. The initiative and design of a more reliable and safe system started in the late fifties when the first-generation CALM and SALM systems were deployed by two operators. In 1959, Shell installed its own patented CALM buoy in Malaysia and ten years later ESO established the first SALM buoy in Libya.
In the past 40 years much has changed in the Single Point Mooring (SPM) market. Due to specially developed techniques, SPM systems are deployed on more and more complex locations. A SPM system is a buoy anchored offshore that serves as a mooring point and interconnects tankers to load or offload gas or fluid products, fluids such as oil are transferred via flowlines and subsea pipelines between the shore and the SPM system.
A typical Catenary Anchor Leg Mooring (CALM) system consists of the mooring buoy, chain and anchor system, mooring assemblies and floating and submarine hose strings. Today this is the most commonly used type of SPM. There are two types of CALM buoys, the turntable types, and the turret types.
In the turntable configuration, the body that provides the buoyancy is geostatically fixed with the mooring lines to the seabed. The upper part can rotate freely, allowing to weathervane. For a turret buoy, the turret is geostatically fixed with mooring lines to the seabed. The body that provides the buoyancy can rotate around the turret thus allowing to weathervane.
Optimising for safety
There have been notable incidents where failures in the system led to leakages that are both costly and have environmental consequences. According to Mike Young, owner of Marsol International, these accidents can be avoided if operators fully optimize their operations by taking into account local conditions and operating processes.
One of the most effective tools that specialist Marsol International utilize when it comes to design or optimization of an offloading terminal is the meteorological and oceanographic (metocean) analysis. Metocean is concerned with the winds, waves, currents, tides, temperatures and sea conditions and the impact these parameters have on the design, installation, and operation of offshore facilities.
Metocean criteria are part of an overall design recipe to ensure structural integrity and reliability. Other elements that are considered include loads, structural analyses, design rules, safety factors, workmanship, quality control procedures and national requirements.
A good understanding of metocean conditions reduces uncertainty in engineering specifications, provides help in operational planning, leads to reduced costs, and enhances safety and operational efficiency.
“The influencing factors are the geography, weather, environmental concerns and operating parameters,” Young said. “We consider all of these and if any of these change the design can be called into question and it needs to be reassessed. Quite often people don’t notice the change, as the design life can be 25/35 years or more, they take things as a norm and that everything is okay.”
Moving mountains
Young points to a project that Marsol carried out several years ago. “A design was produced based on some of the critical factors being weather, waves and current,” he said. “That information informs you how the buoy is going to behave, and from that you can start to calculate fatigue, for example. In this project, the local conditions were altered by changes to the landscape.
“There was a land reclamation project undertaken that required rocks to extend the shoreline, so the mountains disappeared and that changed the wind direction and behavior.
“That was the first part. Then they dumped the rock in the sea to reclaim the land. They created a sea wall that in turn created a refracted wave that changed the wave action and currents. The behavior of the buoy and the design parameters were no longer relevant, resulting in abnormal wear.
“Marsol considered the entire scope of the project, collected data through the water column and looked at the system’s behavior through the use of cameras and modeling. Armed with this information we applied our operational engineering experience to determine the root cause and discovered a simple and cost-effective solution.”
Developing local knowledge
When it comes to maintaining an offshore terminal, operators follow the Oil Companies International Marine Forum (OCIMF) guidelines for testing. Young explained these are not hard and fast regulations but more a guideline.
“An interesting thing is that many people take these guidelines as a regulation and follow them to the letter,” he said. “These guidelines are generic, however every site has a different set of characteristics that are impacted by weather, local conditions, and operating parameters. If you go in a straight line you can be wasting a lot of money and be spending your OPEX dollars on the wrong thing because, at that specific site, the point of failure may be different.
“The problem is what we have been saying on many occasions is that these guidelines don’t tell the history on site. When we test a site we analyze everything according to the OCIMF guidelines. In addition to this, over time we can collect operational data that allows us to develop our own site-specific guidelines, which are much more suitable and offer better outcomes both in terms of safety and operational efficiency for that particular system.”